Dies hat sich aufgrund des von der Europäischen Kommission verbindliche Ziel, mindestens 25 % recycelte Kunststoffe in Neufahrzeugen zu verwenden, geändert. Um diese Vorgabe erfüllen zu können, sind künftige zusätzliche Verwertungsverfahren notwendig. Eines der Hauptziele ist, dass 25 % der in Neuwagen verwendeten Kunststoffe aus rezyklierten Materialien stammen sollen, ein Viertel davon aus Altfahrzeugen. Insgesamt sollen 30 % der Kunststoffe aus verschrotteten Fahrzeugen recycelt werden, während es heute nur 19 % sind.
Die Vorschrift sieht vor, dass die Automobilhersteller den Demontagebetrieben detaillierte Anweisungen für den Austausch und die Entfernung von Bauteilen nach Ablauf der Nutzungsdauer eines Fahrzeugs geben. Ein durchschnittliches Auto enthält zwischen 150 und 200 kg Kunststoff.
Die Maßnahmen würden die Kohlenstoffemissionen bis 2035 um ~12,3 Millionen Tonnen jährlich reduzieren, so die Kommission. Sie schätzt, dass die Regelung bis 2035 zu Nettoeinnahmen in Höhe von 1,8 Milliarden Euro führen wird.
Werden Fahrzeuge im Schredder zerkleinert, entsteht einerseits eine wertvolle Metallfraktion, bestehend aus Eisen- und Nicht-Eisen-Metallen. Andererseits erhält man die sogenannte „Schredder-Leicht-Fraktion“, in der alle anderen Materialien wie Kunststoffstoßstangen, Sitzpolster, Armaturentafeln, Dachhimmel und vieles mehr in zerkleinerter Form vorliegen. Außer diesen Produkten findet man dann noch zusätzlich einen erheblichen Anteil an Gummi, der von den z. T. zusammen mit der Karosserie zerkleinerten Autoreifen stammt. Die nach Abtrennung der „Leichtfraktion“ entstehenden Hartkunststofffraktionen beinhalten immer noch die unerwünschten Gummistückchen aus zerkleinerten Reifen. Diese Gummistücke liegen zum Teil im gleichen Dichtebereich wie die Thermoplaste und können deshalb nicht mit Dichte-Trenn-Verfahren separiert werden.
Zur Abtrennung dieser Gummifraktion, die aufgrund des hohen Anteils an Ruß mindestens halbleitend ist, setzt man elektrostatische Separatoren vom Typ Hamos KWS ein. Der größte Teil der Gummifraktion wird zusammen mit anderen leitfähigen Produkten (z. B. feuchtes Holz!) abgetrennt. Der übrigbleibende Hartkunststoff ist anschließend nahezu gummifrei. Durch eine nachfolgende Kombination aus nassen und trockenen Aufbereitungsverfahren können aus solchen Mischkunststoffen sortenreine Fraktionen wie ABS, PS und PP erzeugt werden. Aber auch wenn diese Schredder-Fraktionen „unsortiert“ in die thermische Verwertung gehen, ist die möglichst vollständige Gummiabtrennung sinnvoll, um den bei der Verbrennung unerwünschten Schwefelgehalt zu reduzieren.
Probleme mit Elastomeren
Allen Gummiarten und –sorten ist gemeinsam, dass sie Duroplaste sind, d. h. dass sie bei der Weiterverarbeitung von Kunststoff-Recyclaten in der Kunststoff-Schmelze nicht aufschmelzen. Sie verbinden oder verschmelzen demnach nicht mit dem eigentlichen Kunststoff-Produkt und führen im fertigen Teil zu Löchern, Werkzeugbeschädigungen und vieles mehr.
Mit modernen Schmelzefiltern, die am Ende eines Extruders eingebaut sind, lässt sich ein bestimmter Anteil der Elastomere aus der Kunststoffschmelze herausfiltern. Dazu spielt das Gesamtsystem, bestehend aus Extruder mit richtiger Schmelzetemperatur, richtigem Druck im Extruder sowie die Filterfeinheit des nachfolgenden Schmelzefilters eine große Rolle. Werden allerdings diese Parameter falsch eingestellt, ist der Prozentsatz des Gummis im Mahlgut zu hoch oder beispielsweise der Druck im Extruder zu hoch, werden die Elastomer-Stückchen durch den hohen Druck einfach durch den Schmelzefilter hindurch gedrückt und landen im Granulat oder im Fertigprodukt. So genügen schon kleinste Verunreinigungen von Gummi im Mahlgut, um ein Produkt oder ein extrudiertes Rezyklat ganz oder teilweise unbrauchbar zu machen. Daraus folgt nunmehr, dass die saubere und möglichst vollständige Abtrennung der Elastomer-Fraktion aus Kunststoffmahlgut ein entscheidender Schritt bei der Erzielung sauberer Kunststofffraktionen ist.
Separationsmöglichkeiten für Gummipartikel
Hamos hat verschiedenste Verfahren entwickelt, um solche „Gummifraktionen“ aus zerkleinerten Kunststoff-Mahlgütern abzutrennen. Alle Verfahren arbeiten optimal, wenn die Mahlgüter im Korngrößenbereich < 10 mm vorliegen und vorher sorgfältig entstaubt wurden.
Leitfähige Elastomere
Viele Elastomere werden mit Ruß gefüllt oder mit Pigmenten aus Ruß schwarz eingefärbt. Dieses sogenannte ‚Carbon black‘ ist der beispielsweise im Reifen am weitesten verbreitete Zuschlagstoff. Bei der Abtrennung der Gummifraktion aus dem Kunststoff macht man sich die Tatsache zunutze, dass mit Ruß gefüllte Partikel elektrisch leitfähig sind, während die Kunststoffe selbst aus Nichtleitern bestehen. Zu beachten ist, dass sowohl Gummi als auch bestimmte Kunststoffe zum Teil gleiches spezifisches Gewicht haben und deshalb Dichtetrennverfahren nicht erfolgreich sind. Auch die Farbsortierung funktioniert nicht – alles ist schwarz!
Zur Leiter-Nichtleiter-Trennung lassen sich aber elektrostatische Separatoren einsetzen. Die gummihaltigen Kunststoff-Mahlgüter werden dabei auf eine rotierende Separations-Walze aufgegeben und über eine Hochspannungselektrode im elektrischen Feld aufgeladen. Die Entladung der Partikel auf der geerdeten Separationswalze erfolgt dann abhängig von der Leitfähigkeit der Produkte. Gute Leiter wie rußgefüllte Gummipartikel entladen sich sehr schnell und fallen ab, während Kunststoffe als gute Isolatoren sich sehr langsam entladen und an anderer Stelle absepariert werden. Solche elektrostatischen Separatoren sind in der Recycling-Industrie sehr weit verbreitet. Standardgeräte können aus bis zu 1.800 kg/h „verunreinigtem Granulat“ die Gummifraktion abtrennen.
Nichtleiter-Nichtleiter-Trennung
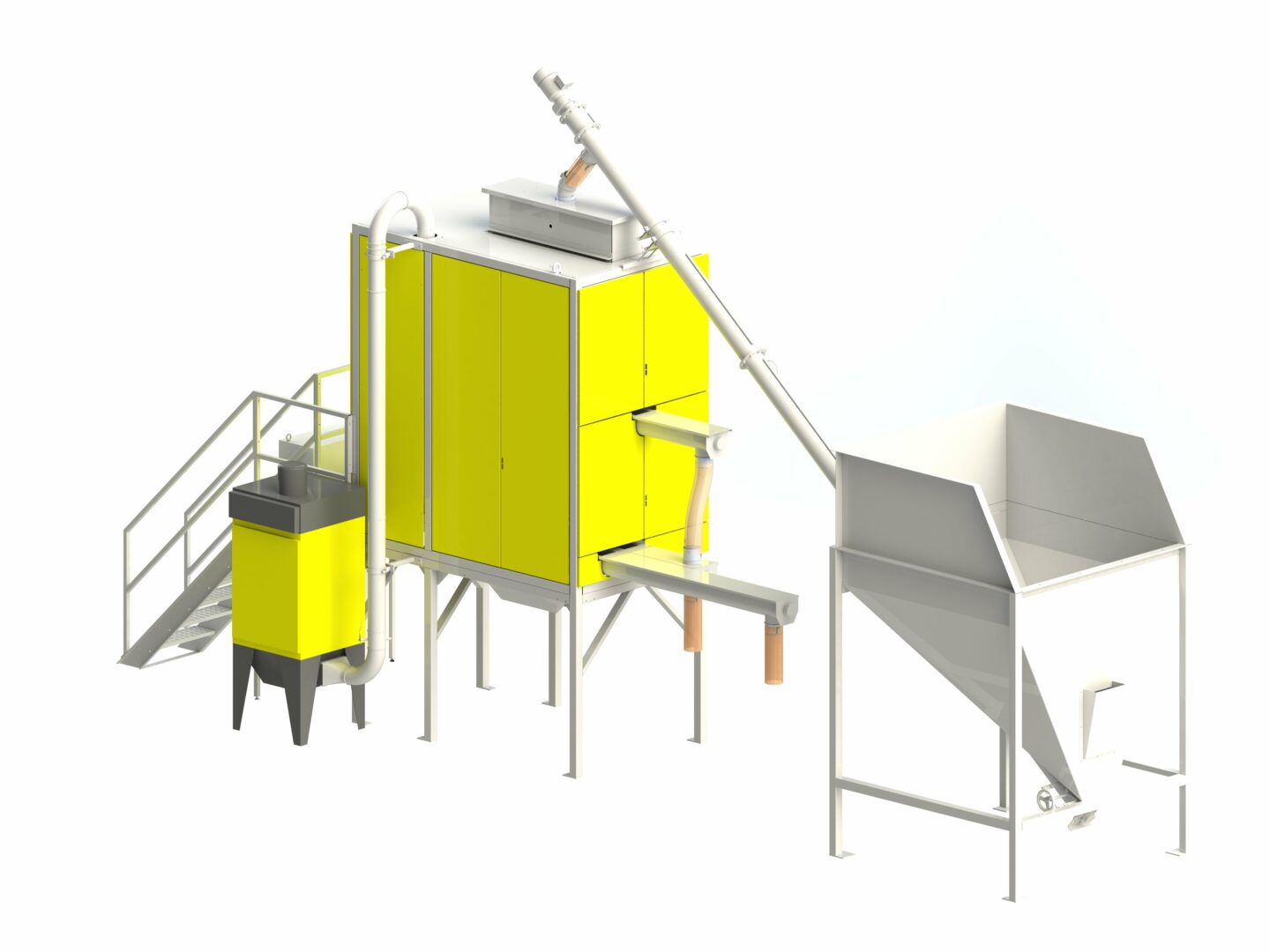
Elektrostatischer Separator Hamos KWS. Copyright: Hamos
Schwieriger wird es, wenn sowohl Gummi als auch das Kunststoffmahlgut aus nichtleitenden Materialien bestehen. In diesem Falle leisten die elektrostatischen Kunststoff-Kunststoff-Separatoren hervorragende Arbeit. Durch eine spezielle Auflade-Einrichtung innerhalb des Gerätes werden die Kunststoffe etwa positiv, Gummi und andere Elastomere beispielsweise negativ aufgeladen. Die Abtrennung erfolgt anschließend in einem Elektrodensystem, das mit Hochspannung arbeitet. Positiv geladene Teilchen werden beispielsweise durch eine negative Elektrode angezogen und umgekehrt. Standardgeräte trennen bis zu 1.000 kg/h, höhere Durchsätze können durch Parallelschalten mehrerer Geräte realisiert werden.
Abtrennung von Schäumen, Silikonen, usw.
Eine Reihe von Gummiarten, Silikonen und insbesondere Schaumgummis lassen sich mit herkömmlichen Verfahren der Separationstechnik nicht abtrennen. Die Gummi-Separations-Systeme von Hamos nutzen dabei unterschiedliche physikalische Parameter zwischen Kunststoff und Gummi zur Separation aus. Der Hamos RSS Separator trennt ca. 75 – 95 % der störenden Gummifraktion auf trockenem Wege ab. Durchsätze bis zu 1.000 kg/h sind mit Standardgeräten problemlos möglich.
Recycling von entnommenen Autoteilen
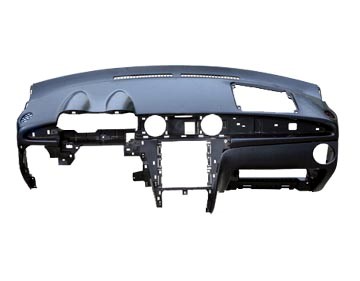
Die Reinheit ist so hoch, dass dieses Produkt wieder direkt in neue Armaturentafeln eingearbeitet werden kann. Copyright: Hamos
Die elektrostatische Separationstechnik eignet sich für ein Recycling von Armaturentafeln. Bei der Produktion von Cockpits und Instrumententafeln für Autos entsteht produktionsbedingt eine Abfallmenge von bis zu 20 Prozent. Im Wesentlichen handelt es sich dabei um hochfeste Trägerwerkstoffe wie beispielsweise SMA mit Glasfaser-Verstärkung, beschichtet mit PU-Schaum und einer „Deckhaut“, zum Beispiel aus PVC oder PU. Insbesondere das SMA ist ein sehr hochwertiger und teurer Kunststoff, der allein schon aus Wirtschaftlichkeitsgründen recycelt werden sollte, damit die wertvollen Kunststoffe nicht verloren gehen. Problematisch dabei ist allerdings, dass in den meisten Fällen alle drei Kunststoffe SMA, PU-Schaum und Deckschicht schwarz eingefärbt sind.
Die Produktionsabfälle werden zerkleinert und in einer Schneidmühle gemahlen. Durch die Reibung in der Mühle wird das PU praktisch vollständig vom SMA und vom PVC abgetrennt und kann anschließend problemlos durch Windsichtung separiert werden. Das Gemisch aus schwarzem SMA mit schwarzem PVC wird nun elektrostatisch separiert. Die dabei erzielbaren Reinheiten des SMA liegen bei über 99,5 Prozent. Diese Reinheit ist so hoch, dass dieses Produkt wieder direkt in neue Armaturentafeln eingearbeitet werden kann. Auch das Weich-PVC kann aufgrund seiner hohen Reinheit wieder problemlos in neue Produkte eingearbeitet werden.
Teile von Lüftungs- und Klimaanlagen im Pkw, die nicht direkt im Blickfeld der Passagiere liegen, werden zu nahezu 100 Prozent aus schwarzen Kunststoffen gefertigt. Funktionsbedingt kommen dazu verschiedene technische Kunststoffe zum Einsatz. Häufig werden dabei auch Verbundmaterialien eingesetzt, bei denen beispielsweise an eine Lüftungsklappe aus Glasfaser-verstärktem PP eine elastische Dichtlippe aus TPU oder EPDM angespritzt wird. Beim Recycling von Produktionsabfällen bereiten diese von den Gummilippen herrührenden Verunreinigungen große Probleme und verhindern, dass das Rezyklat wieder verwendet werden kann.
Bei der Zerkleinerung der Materialien in einer Schneidmühle wird die Gummilippe fast vollständig durch die Reibung innerhalb der Schneidmühle abgelöst. Das Mahlgut wird entstaubt und anschließend elektrostatisch separiert. Man erhält eine hoch konzentrierte PP-Fraktion. Die schwarze Farbe sowohl der Funktionsteile als auch der EPDM-Dichtungen spielt dabei keine Rolle.