Kategorie: Prozessinnovationen für den Klimaschutz. Das RECYCLING magazin sprach mit dem Leiter der Forschungs- und Entwicklungsabteilung, Dr. Wolfgang Dienemann, über das Konzept und an welchen Themen das R&D-Team darüber hinaus arbeitet.
Vielleicht hat sich der ein oder andere über den Namen gewundert, der stark an HeidelbergCement erinnert – das Gefühl trügt nicht. HeidelbergCement hat sich zum 20. September 2022 in Heidelberg Materials umbenannt. Der Bereich Zement spielt weiterhin eine große Rolle, macht heute aber nur rund 50 Prozent des Gesamtumsatzes aus. Dafür haben Aggregates, also Zuschlagstoffe, an Bedeutung gewonnen, ebenso Transportbeton und Asphalt. Im Wort „Materials“ stecke eben besser drin, dass man breiter aufgestellt ist, so Chef-Entwickler Dienemann. Das gilt auch für den Klimaschutz: Als erstes Unternehmen weltweit will Heidelberg Materials 2024 CO2-freien Zement anbieten. Und bis 2030 lautet das Ziel, mithilfe bereits gestarteter CCUS-Projekte den CO2-Ausstoß um insgesamt 10 Millionen Tonnen zu reduzieren. Als einer der weltweit größten integrierten Hersteller von Baustoffen hat das Unternehmen mit mehr als 51.000 Beschäftigten an 3.000 Standorten in über 50 Ländern auf jeden Fall eine Hebelwirkung.
CO2-intensive Herstellung von Zement
Beton ist ein vielseitig einsetzbarer Baustoff und unverzichtbar für unsere Infrastruktur. Ob Estrichbeton, Fließbeton, Sichtbeton, Nass- und Spritzbeton – Beton ist allgegenwärtig. Als „Transportbeton“ wird er entsprechend gemischt und direkt zur Baustelle geliefert. Beton besteht aus Sand und Kies und dem Bindemittel Zement und weist selbst einen sehr niedrigen CO2-Fußabdruck auf. Nicht so der Zement, für dessen Herstellung zwei CO2-intensive Prozesse nötig sind. Im Zementwerk werden Kalkstein und Ton zu einem feinen Pulver vermahlen und bei hohen Temperaturen bei 1.450 Grad Celsius gebrannt, wodurch die Körner verkleben (Sinterung) und sogenannter Zementklinker entsteht. Manchmal werden noch Quarzsand und eisenoxidhaltige Stoffe zugemischt, um die gewünschte Zusammensetzung oder eine bessere Sinterung zu erzielen. Der Klinker wird nach dem Abkühlen erneut gemahlen – zu Zement. Der Brennvorgang ist durch den Einsatz fossiler Rohstoffe (Kohle) CO2-intensiv, aber auch der stattfindende chemische Prozess selber: Durch die hohen Temperaturen wird der Kalkstein (Calciumcarbonat CaCO3) entsäuert, das Kohlendioxid (CO2) entweicht und man erhält das für die Zementherstellung gewünschte Calciumoxid (CaO). Das Ausmaß dieses Problems wurde von der Universität Mainz, wo Chemiker am Thema Kohlendioxidausstoß bei der Zementproduktion forschen, in einer Pressemitteilung vom 21.11.2021 wie folgt beschrieben: Für „jedes produzierte Molekül Kalziumoxid (CaO)“ werde „ein Molekül des Treibhausgases CO2 freigesetzt. Bei einer Weltjahresproduktion von rund 4,5 Milliarden Tonnen Zement sind das immerhin rund 2,7 Milliarden Tonnen CO2. Dies entspricht etwa der Hälfte der CO2-Emissionen aus dem Verkehr.“
Konzept ReConcrete-360°
Mit dem Projekt ReConcrete-360° wollen Dienemann und sein Team den Wertstoff Kalziumoxid aus Abbruchbeton zurückgewinnen und erneut bei der Herstellung von Zement verwenden – dadurch lässt sich ein Teil primärer Kalkstein ersetzen, aus dem schon mal kein weiteres CO2 emittiert wird. Dafür mussten allerdings neue Technologien gefunden werden. Für das bereits erhältliche Produkt EcoCrete von Heidelberg Materials wird recycelte Gesteinskörnung verwendet, auf Basis heutiger Recyclingtechnologie. Für ReConcrete galt es aber, noch einen Schritt weiter zu gehen. „Beim herkömmlichen Brechen des Materials und Fraktionieren über Siebanlagen klebt noch sehr viel Zementstein am Sand und Kies, der damit beim Recyclingprozess als Störstoff gilt. Verwendet man dieses Material erneut im Beton, saugt es viel Wasser auf, man benötigt mehr Zement und Zusatzmittel, darunter leidet die Qualität. Wir benötigten deshalb ein besseres Aufbereitungsverfahren, in dem Scherkräfte mit deutlich geringeren Drücken aufgewendet werden, um die Oberfläche der Sand- und Kieskörner vom Zementstein zu befreien“, erklärt Dienemann.
Rückgewinnung von Sand und Kies
Auf der Suche nach dieser Technologie wurde die R&D-Abteilung bei Equipment aus der Erzaufbereitung fündig. Hier werden solche Prozesse mit Scherbeanspruchung benötigt, um zum Beispiel Erz von den Seitenmineralien zu befreien. Normalerweise werde Brechsand, so Dienemann, heute nicht wieder im Beton eingesetzt, sondern gehe nur in untergeordnete Anwendungen oder werde im schlimmsten Fall deponiert. Den Sand hingegen könne man so aufbereiten, dass er einem Natursand vielleicht nicht 100 Prozent gleichwertig ist, aber diesem doch so nahe kommt, dass man sehr große Anteile wieder in den Beton zurückführen könne. Bei der gröberen Fraktion, dem Kies, ginge dass umso leichter. Dienemann: „Da kommen wir wirklich auf Austauschraten von 100 Prozent ohne Qualitätsbeeinträchtigung. Damit schließen wir den Stoffkreislauf von Sand und Kies.“ Im ersten Halbjahr 2023 soll eine erste Anlage in Polen installiert werden und in Betrieb gehen, „um dann wirklich großtechnische Erfahrung zu sammeln“, erklärt Dienemann, und fährt fort: „Wir werden die Ersten sein, die eine solche Anlage im industriellen Maßstab erproben, und wir reden dann von 200.000 Tonnen Beton-Aufbereitung pro Jahr, einer normalen Größenordnung für ein Beton-Recyclingwerk.“
Zementstein oder RCP
Als Neben- beziehungsweise, je nach Standpunkt, Zielprodukt gewinnt Heidelberg Materials auch den „Störstoff“ Zementstein zurück: „Recycled Concrete Paste“ – kurz RCP. Zementstein hat die Eigenschaft, wieder CO2 aus der Atmosphäre aufnehmen zu können. Grundsätzlich karbonatisiert Beton bis zum Ende seiner Nutzungsdauer als Bauteil. Circa 20 Prozent des während der Klinkerherstellung emittierten CO2 werden so im Laufe seines Lebens als Baustoff auf natürliche Weise wieder im Beton fixiert. „Diese Grundeigenschaft der Karbonatisierung machen wir uns zunutze und beschleunigen diese aber massiv. Wir haben als Ausgangspunkt mit RCP ein äußerst feines Pulver, das CO2 ohnehin schon wesentlich besser aufnehmen kann. Und wir lassen das nicht in der natürlichen Umgebungsluft bei 460 ppm CO2 karbonatisieren, sondern setzen das Pulver unseren eigenen Ofenabgasen aus, die 20 Prozent CO2enthalten. Somit schaffen wir diese Karbonatisierung deutlich schneller.“ Der Zementstein lasse sich somit wiederverwerten.
Drei Verwertungswege
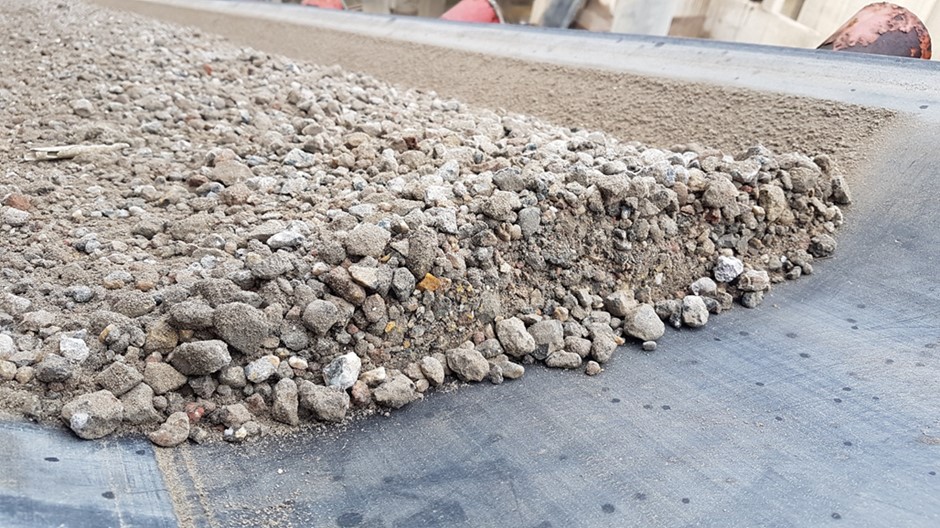
Durch selektive Trennung wird der Altbeton mit geringeren Drücken aufbereitet und die Oberfläche der Sand- und Kieskörner werden sauber vom Zementstein getrennt. Copyright: Heidelberg Materials
Dies geschieht laut Dienemann auf dreierlei Weise: RCP kann als Kalksteinersatz wieder im Ofen eingesetzt werden. Da es schon mal entkarbonatisiert war, bringt es deutlich weniger CO2-Fracht mit. Etwa 20 Prozent primärer Kalkstein ließe sich so einsparen; mehr nicht, da auch Sandpartikel enthalten seien, wodurch ab einem bestimmten Punkt die Chemie nicht mehr stimmen würde. Alternativ könne man das Material, aufgemahlen, auch direkt als Zementkomponente verwenden, auch hier schätzt Dienemann 20 Prozent Einsparung als realistisch ein. Oder – im Sinne einer Art CO2-Sequestrierung – den Karbonatisierungsschritt als dritte Option, mit vielleicht 35 Prozent Ersatz für primären Kalkstein, indem man aus dem Kalkstein wieder Kalkstein macht. Damit schließt sich der CO2-Kreislauf. Die während der Klinkerherstellung freigesetzten Prozess-Emissionen lassen sich zu 80 bis 90 Prozent innerhalb weniger Minuten im RCP wieder speichern. Das konnte das R&D Team bereits grob im großtechnischen Maßstab in Zementwerken nachweisen, allerdings noch mit Anlagen, die dafür nicht designt waren. „Eine Umsetzung dieses Karbonatisierungsschritts im großtechnischen Maßstab planen wir als Commercial-Scale-Pilotanlage für 2025“, so Dienemann.
„Karbonatisierung war bislang für Betonfachleute immer etwas Böses, weil sie auf Dauer die pH-Pufferwirkung im Beton stört, die den Bewehrungsstahl schützt“, erinnert sich Dienemann. Den Gedanken, am Ende des Lebenszyklus von einem Bauwerk diesen Prozess positiv umzukehren, der ist ihm und seinem Team vor circa fünf Jahren gekommen. Das R&D-Team begann mit kleinen Experimenten im Gramm-Maßstab. „Und ab nächstem Jahr steht da eine Anlage mit ein paar 100 Tonnen am Tag. Das ging jetzt schon vergleichsweise schnell“, freut sich Dienemann.
Ein weiterer Nebeneffekt: Zementstein besteht nicht nur aus Kalk, sondern hat auch Aluminium- und Siliziumkomponenten. Diese werden bei dem Karbonatisierungsschritt wieder freigesetzt und liegen in einer glasigen Form vor. Sie reagieren dann wie Puzzolan, wie eine Flugasche oder ein vulkanisches Gestein, mit dem Kalziumhydroxid, was bei der Klinkerhydratation freigesetzt wird. „Damit lassen sich noch mal 20 bis 35 Prozent Klinker ersetzen. Ich habe also eine doppelte Hebelwirkung“, erklärt Dienemann. „Die CO2-Einbindung einerseits und der Klinkerersatzstoff andererseits, sodass sich pro Tonne von diesem Zementstein, grob gerechnet, eine Tonne CO2 einsparen lässt.“
Kalzinierter Ton als Klinkersubstitut
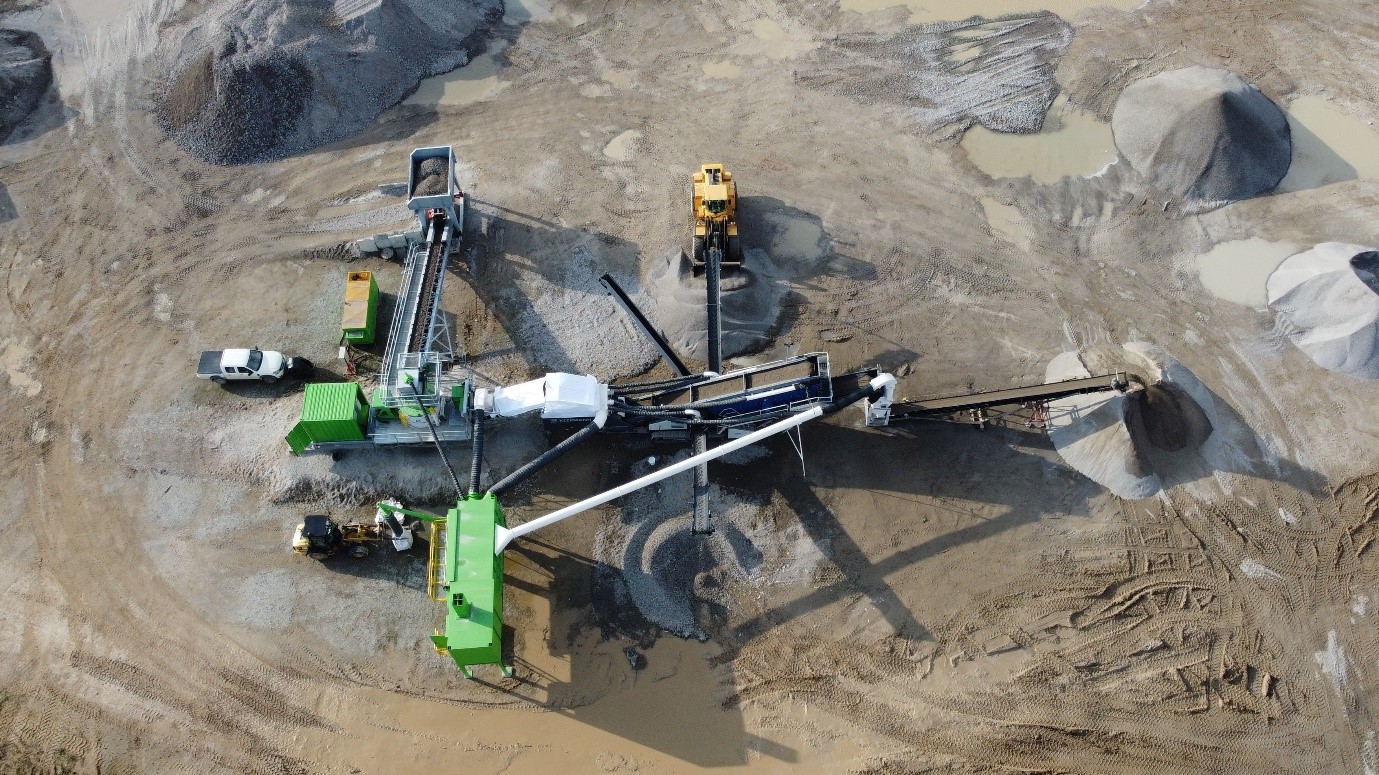
Im ersten Halbjahr 2023 soll eine erste großtechnische Anlage für selektive Trennung in Polen installiert werden. (Symbolbild) Copyright: Heidelberg Materials
Heidelberg Materials investiert auch in kalzinierte Tone. Im Mai 2022 gab das Unternehmen bekannt, in ein Joint Venture in Ghana investiert zu haben. Dort soll das weltweit größte Werk für kalzinierten Ton entstehen, mit einer Kapazität von mehr als 400.000 Tonnen pro Jahr. Die CO2-Emissionen aus der Kalzinierung von Ton liegen deutlich unter den Emissionen aus der Klinkerproduktion. Durch die Substitution von Klinker durch kalzinierten Ton wird dabei nicht nur der CO2-Fußabdruck des Zements erheblich reduziert. Laut Unternehmen könnten besonders westafrikanische Länder ohne größere Kalksteinvorkommen so auch unabhängiger von Klinkerimporten werden.
Weitere R&D-Felder
Ein weiteres Themenfeld kommt aber noch hinzu: Die Suche nach neuen reaktiven Bestandteilen. In den nächsten Jahren werden bisher so gebräuchliche Stoffe wie Hüttensand aus der Eisenherstellung oder Flugasche aus den Kraftwerken deutlich reduziert verfügbar sein. Dienemann: „Auch die Stahlindustrie hat eine Dekarbonatisierungsstrategie, und Kohlekraftwerke sollen perspektivisch abgeschaltet werden. Also brauchen wir Riesenmengen an alternativen Zementbestandteilen.“ Heidelberg Materials ist hier im Austausch mit der Stahlindustrie, um künftige Nebenprodukte zu identifizieren, die einmal bei der DRI-Technologie abfallen, Direct Reduced Iron, „auf dem Wasserstoff-Weg sozusagen“, erläutert Dienemann. „Hier arbeiten wir beispielsweise mit ThyssenKrupp an einem Projekt.“
Auch an Themen wie 3D-Druck und Ultra-High-Performance Concrete, bei dem für die gleiche Bauweise weniger Beton eingesetzt werden kann, forscht Dienemann mit seinem R&D-Team. Ebenso wird an der Karbonatisierungshärtung gearbeitet.
CO2-Kreislauf zu Beginn
„Man kann die Karbonatisierung vom Zement nicht nur am Ende der Lebenszeit durchführen, sondern kann den CO2-Kreislauf gleich am Beginn des Lebenszyklus vom Beton-Produkt einsetzen lassen“, erklärt Dienemann, der an einem vom BMBF geförderten Projekt arbeitet. Pflastersteine sollen in einem frühen Stadium karbonatisiert werden. Das Projekt ist schon im halbtechnischen Maßstab angekommen. Dienemann sieht hier aber das Problem, dass auch Pflasterstein- oder Dachstein-Produzenten investieren müssten. „Die Umsetzung liegt im Fokus unserer Kunden und nicht direkt beim Baustoffhersteller. Aber wir wollen verstehen, wie man diesen Prozess im Betonmischdesign optimieren und effizient gestalten kann.“
Forschungsansätze weltweit
„Es gibt viele Firmen, Universitäten oder Start-ups, die nach neuen Ansätzen suchen. Ob das jetzt die Nutzung von Solarenergie für die Klinkerherstellung ist oder die Einbindung von CO2 in alle möglichen Stoffströme“, erklärt Dienemann. Viele Ansätze werden auch in China verfolgt, auf dessen Konto um die 60 Prozent der CO2-Emissionen der Gesamtzementproduktion gehen. „Hier wird auf der wissenschaftlichen Seite intensiv gearbeitet und erste Zementunternehmen haben dort schon im halbtechnischen Maßstab Carbon-Capture-Technologien eingesetzt“, so Dienemann. „In diesem Feld ist auf jeden Fall auch einiges an Bewegung in der Branche“, so Dienemann abschließend.