Daneben gibt es Rohstoffe, die bereits heute effizient im Kreislauf gehalten werden können. Metalle wie Kupfer, Aluminium oder Nickel sind viel zu wertvoll, um sie zu entsorgen oder illegal zu exportieren. Trimet sprach mit vier Akteuren der Kreislaufwirtschaft. Sie beschreiben am Beispiel von Aluminium, welcher Aufwand betrieben wird, um Recyclingrohstoffe aus Siedlungsabfällen zurück in den Kreislauf zu bringen.
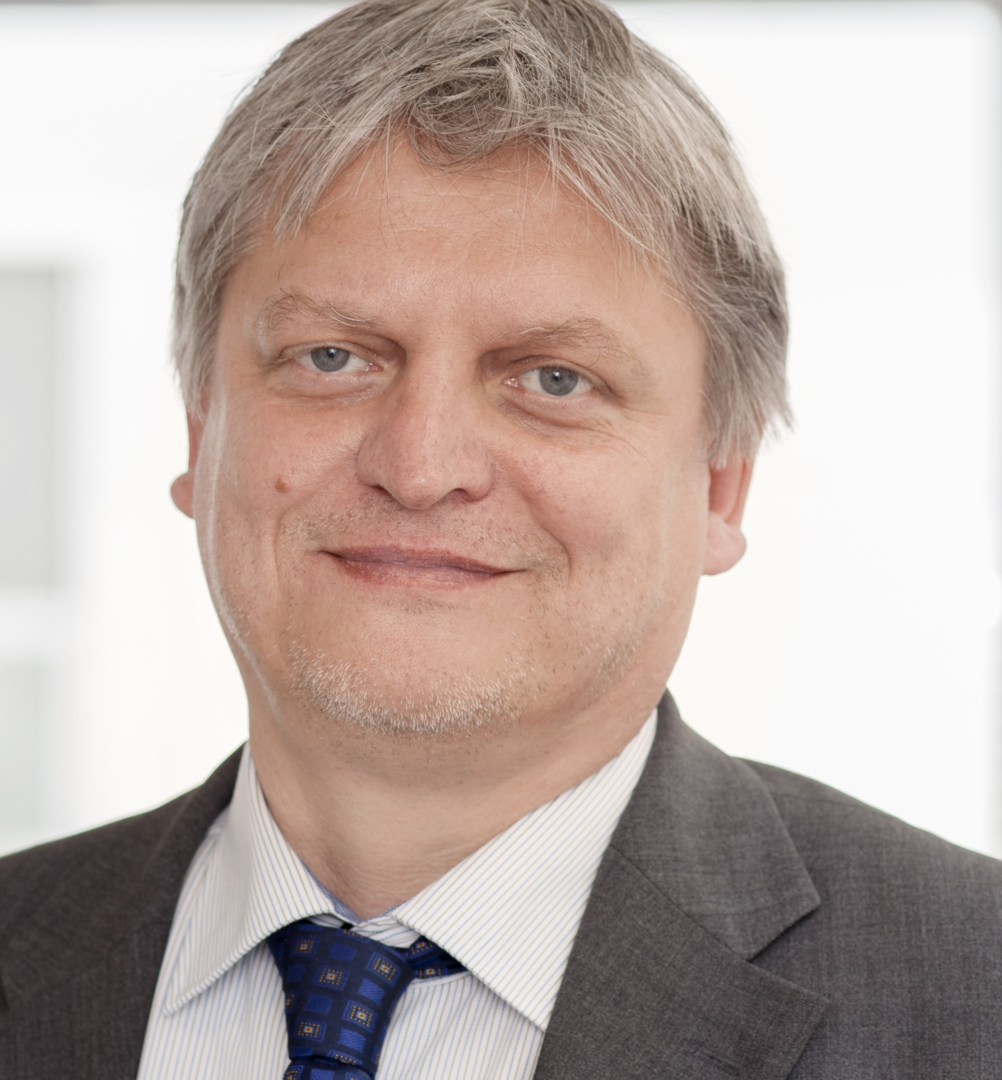
„Die Rolle der thermischen Abfallbehandlung als Schadstoffsenke wird häufig in der Recyclingdiskussion unterschlagen.“ Martin Treder; Stellvertretender Geschäftsführer ITAD, Bild: ITAD
Martin Treder ist stellvertretender Geschäftsführer der Interessengemeinschaft der Thermischen Abfallbehandlungsanlagen in Deutschland (ITAD). In dem Verband sind die Betreiber und Eigentümer von 84 Müllverbrennungsanlagen und Ersatzbrennstoffkraftwerken (TAB – Thermische Abfallbehandlungsanlagen) vertreten.
Herr Treder, die thermische Verwertung kommt gemäß der Abfallhierarchie des Kreislaufwirtschaftsgesetzes erst zum Einsatz, wenn keine Rückgewinnung durch Recycling mehr möglich ist. Welchen Stellenwert hat die thermische Abfallbehandlung in der Kreislaufwirtschaft?
Martin Treder: Die Rolle der thermischen Abfallbehandlung als Schadstoffsenke wird häufig in der Recyclingdiskussion unterschlagen. Wir sagen: „Recycling und Thermik gehen Hand in Hand.“ Ich würde daher einen Schritt vorher ansetzen, es geht ja auch darum, Schadstoffe aus dem Ökosystem auszuschleusen. Leider wird aber häufig aktuell nur der Klimaschutz gesehen. Wenn alle Umwelt-Wirkungskategorien berücksichtigt würden, bekämen Metalle im Abfall einen noch höheren Stellenwert. Neben der Rückgewinnung von Eisen, Kupfer und Aluminium aus den Schlacken spielt die Schadstoffentfrachtung beispielsweise bei Quecksilber im Umwelt-Gesamtnutzen bei TAB eine bisher kaum gewürdigte Rolle. Neben der Schadstoffentfrachtung, der „Unterstützung“ des Recyclings, der Abwärmenutzung in Form von Fernwärme, Prozessdampf, Strom und Folgedienstleistungen wird zukünftig auch die Rückgewinnung von Kohlenstoff mittels „Carbon Capture Technologien“ eine wesentliche Rolle bei der TAB spielen.
Welche Abfallmengen werden jährlich in Deutschland der thermischen Verwertung zugeführt und wie groß ist der Anteil von Metallen?
Treder: Jährlich werden in Deutschland mindestens 50 Millionen Tonnen Abfälle thermisch behandelt. Exakte Zahlen haben wir nicht. Es gibt in Deutschland schätzungsweise 37.000 Anlagen, sie reichen vom kleinen Holzofen bis zur größten TAB in Köln mit einer Kapazität von rund 750.000 Tonnen. Den Metallinput kennen wir nicht genau. Im Rahmen der Hausmüllanalyse des Umweltbundesamtes wurde 2020 ein Metallanteil von zwei Prozent ermittelt. Jedoch ist dies auch nur die halbe Wahrheit, da bei diesen Analysen die Restanhaftungen und die Metalle in Verbunden und in der Feinfraktion unzureichend berücksichtigt wurden. Aber wir können vom Ende her bilanzieren. In den rund 100 TAB werden über 26 Millionen Tonnen Abfälle verbrannt, dabei entstehen rund sechs Millionen Tonnen Schlacke. Aus der Schlacke wurden 2020 noch rund eine halbe Million Tonnen reine Metalle zurückgewonnen, davon über 60.000 Tonnen Aluminium.
Die in den TAB entstandene Schlacke wird im ersten Schritt der Rückgewinnung in einer Schlackenaufbereitungsanlage bearbeitet.
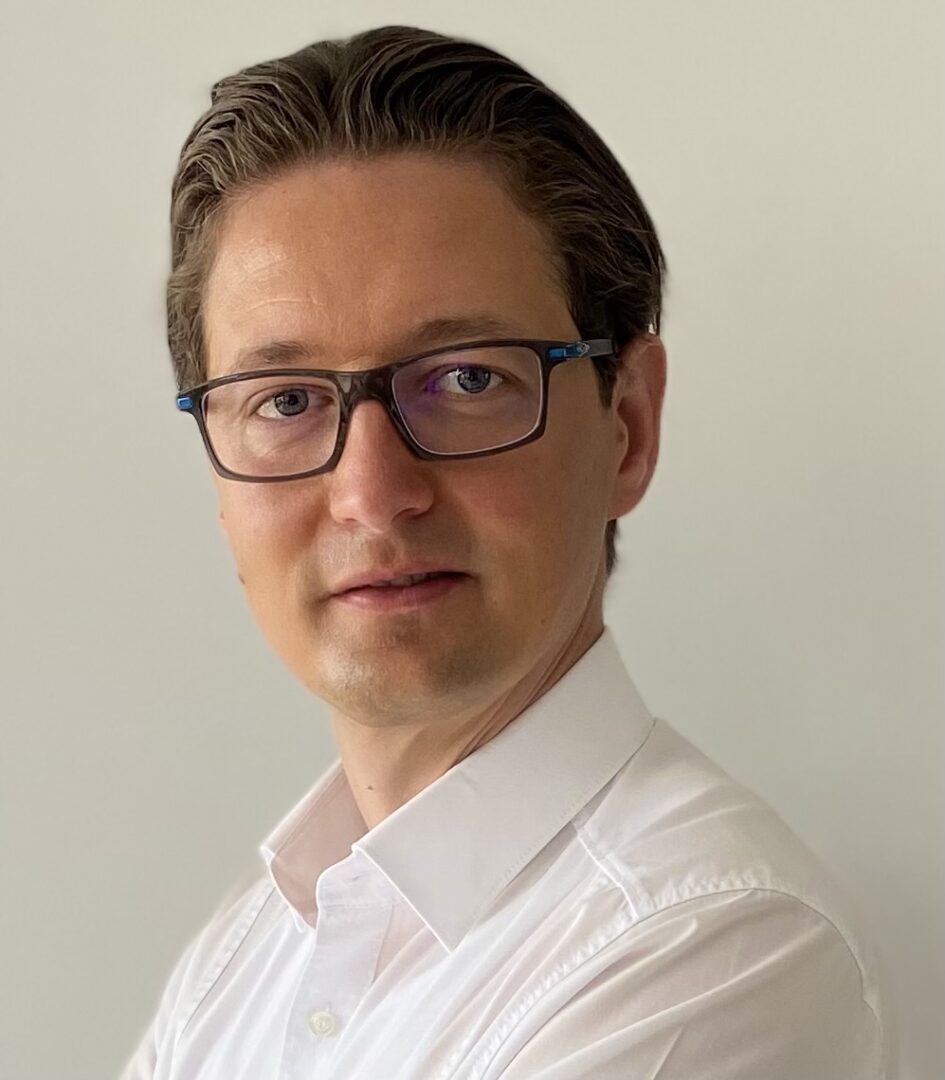
„Leider landet aktuell in Deutschlandnoch ein zu großer Anteil auf Deponien.“ David C. Jörgens; Fachbereichsleiter für mineralische Stoffe bei der Remondis GmbH, Region Südwest Bild. Remondis
David C. Jörgens ist Fachbereichsleiter für mineralische Stoffe bei der Remondis GmbH, Region Südwest. Zu seinem Aufgabenbereich gehört die Unterstützung der Frankfurter Entsorgungs- und Service GmbH (FES), bei der Remondis, neben der Stadt Frankfurt, Gesellschafter ist. Die FES betreibt in Flörsheim-Wicker eine eigene MVA-Schlackenaufbereitungsanlage, in der jährlich mehr als 220.000 Tonnen Rohschlacke aus den Verbrennungsanlagen im Rhein-Main-Gebiet aufbereitet werden. Unter Federführung von Remondis beschreitet man hier beim Schlackemanagement und in der Logistik neue Wege.
Welche Arbeitsschritte finden in der MVA-Schlackenaufbereitungsanlage statt, nachdem die Schlacke angeliefert wurde?
David C. Jörgens: Müllverbrennungsschlacken respektive Rostaschen aus den Verbrennungsanlagen enthalten Metalle, Mineralstoffe und unverbrannte Anteile. Das Ziel einer modernen Aufbereitungsanlage ist es, hier ein bestmögliches Trennergebnis hinzubekommen. Die Metalle (Eisen und Nichteisenmetalle), Mineralstoffe und unverbrannten Anteile sollen möglichst in allen Teilfraktionen, auch den feinen Fraktionen, voneinander getrennt und in separaten Fraktionen aufkonzentriert werden. Spezielles Augenmerk wird hier auf die wertvollen NE-Metalle gelegt, die wir als hochwertige Konzentrate an unseren Partner TSR/Phoenix Mining liefern, der diese dann in einer State-of-the-Art-Aufbereitung gruppenintern aufbereitet und vermarktet. Im Sinne des Recyclinggedankens ist das eine runde Sache für alle Beteiligten. Hier schließe ich auch die Abnehmer, zum Beispiel für das Aluminium, ein. Durch eine verbesserte Abtrenntechnik steigt zudem die Qualität der Restmineralik. Außerdem erschließen sich höherwertige Anwendungsbereiche, sofern dies das Bauregelwerk in Deutschland zulässt.
Was geschieht denn derzeit mit der Restmineralik, und wie könnte man den Einsatz dieser Recyclingrohstoffe im Sinne der Kreislaufwirtschaft unterstützen?
Jörgens: Leider landet aktuell in Deutschland noch ein zu großer Anteil auf Deponien. Die Ersatzbaustoffverordnung wird hier zumindest perspektivisch hoffentlich mehr Verwertungsmöglichkeiten, zum Beispiel im Straßenbau, eröffnen. Gleichzeitig haben wir es aktuell mit einer regional unterschiedlich ausgeprägten Deponieknappheit zu tun. Eine dauerhafte, reine Deponierung großer Mengen kann daher keine nachhaltige und wirtschaftliche Lösung sein. FES und Remondis beschäftigen sich daher schon seit einiger Zeit gemeinsam mit der Entwicklung von hochwertigen Verwertungsmöglichkeiten für bestimmte Teilfraktionen der Restmineralik. In diesem Zusammenhang arbeiten wir mit namhaften Anlagenbauern und Partnern aus der Baustoffindustrie zusammen und binden frühzeitig die Genehmigungsbehörden ein. Ziel ist es, Teilfraktionen der Restmineralik mit einer speziellen Aufbereitungstechnologie weitergehend aufzubereiten und diese als hochwertigen Baustoff beziehungsweise als Ersatz von natürlichen Rohstoffen zu verwenden. Die zunehmende Verknappung natürlicher Baustoffe, die Transportraumverknappung und die sich zuspitzende Energiepreissituation erfordern ein Umdenken im Sinne der Ressourceneffizienz, auch bei der Restmineralik.
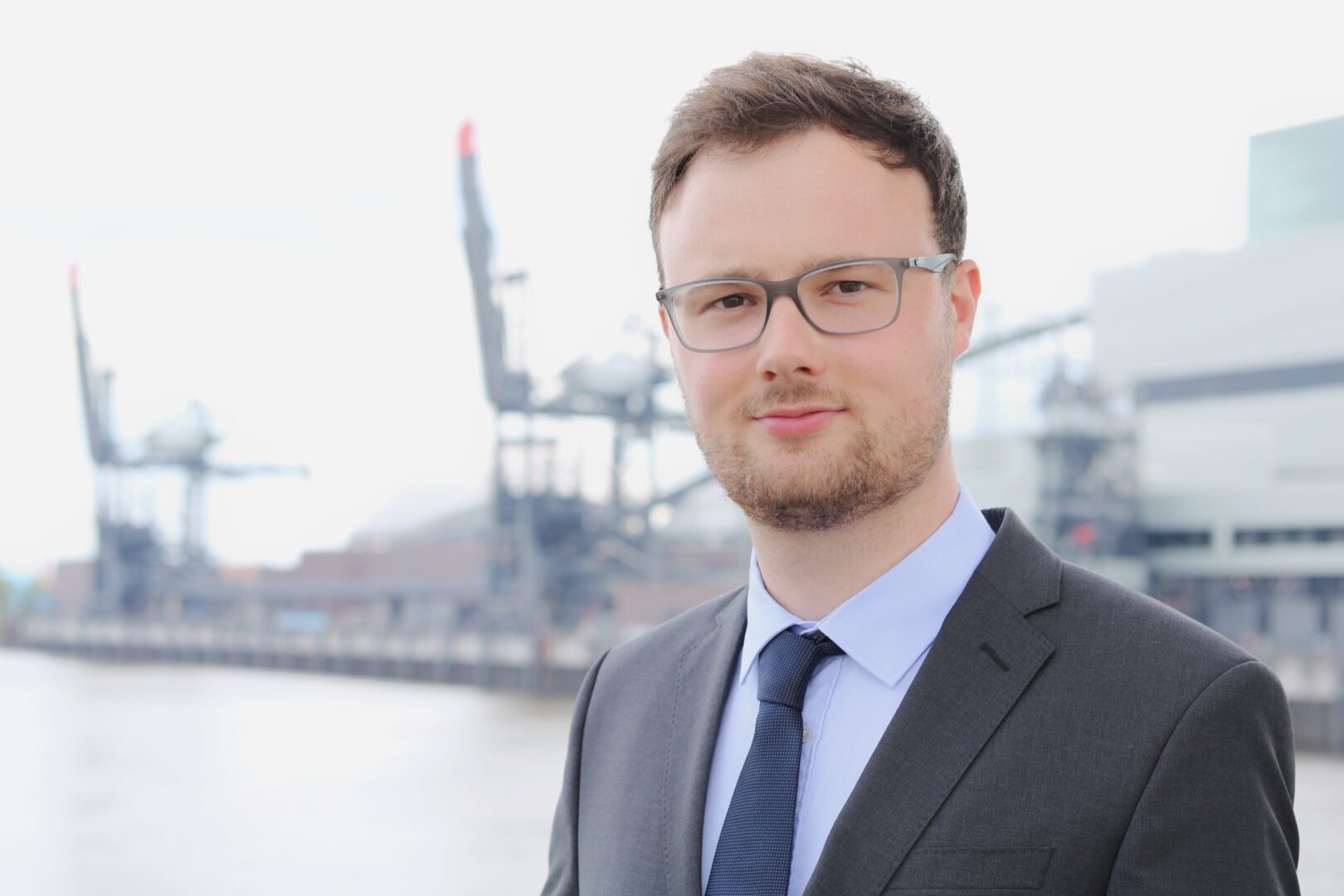
„Der Goldanteil in einer Tonne unserer Kupferfraktion ist höher als in einer Tonne Golderz.“ Matthias F. Hoffmann; Geschäftsführer bei der Phoenix Mining GmbH Bild: Phoenix Mining
Matthias F. Hoffmann ist als Geschäftsführer bei der Phoenix Mining GmbH für die Herstellung von Recyclingrohstoffen aus MVA-Schlacken zuständig. Phoenix Mining hat sich unter anderem auf die Aufbereitung von Nichteisen (NE)-Feinkorn aus Müllverbrennungsanlagen spezialisiert. Das Unternehmen verarbeitet in Dortmund bis zu 10.000 Tonnen jährlich.
Welchen Mehrwert bringt die NE-Feinkornaufbereitung für die Rückführung der Metalle in den Kreislauf?
Matthias F. Hoffmann: Wir gewinnen aus den feinkörnigen NE-Fraktionen aus der Schlackenaufbereitung Aluminium- und Kupferfraktionen zurück. Somit gehen diese nicht verloren und werden wieder dem Rohstoffkreislauf zugeführt.
Wie kann man sich diese Aufbereitung vorstellen?
Hoffmann: Wir schließen das Inputmaterial mechanisch so auf, dass die Metalle von der nicht metallischen Fraktion separiert werden können. Im nachgeschalteten automatisierten Prozess nutzen wir unter anderem die unterschiedlichen elektrischen Leitfähigkeiten und Dichten der Metalle, um diese in eine aluminium- und kupferhaltige Fraktion zu trennen.
Was ist das Besondere an den Kupferfraktionen?
Hoffmann: Unsere Kupferfraktionen enthalten Spuren von Gold, Silber, Platin und Palladium. Diese stammen zum Beispiel aus Elektrogeräten und werden in der Kupferhütte ebenfalls zurückgewonnen. Der Goldanteil in einer Tonne unserer Kupferfraktion ist beispielsweise höher als in einer Tonne Golderz und somit ein sehr gutes Beispiel, wie durch Recyclingrohstoffe die Umwelt geschont werden kann. Das Aluminium aus der NE-Aufbereitung kann im Anschluss ebenfalls direkt als umweltfreundlicher Recyclingrohstoff zum Beispiel bei Schmelzwerken im Umfeld eingesetzt werden.
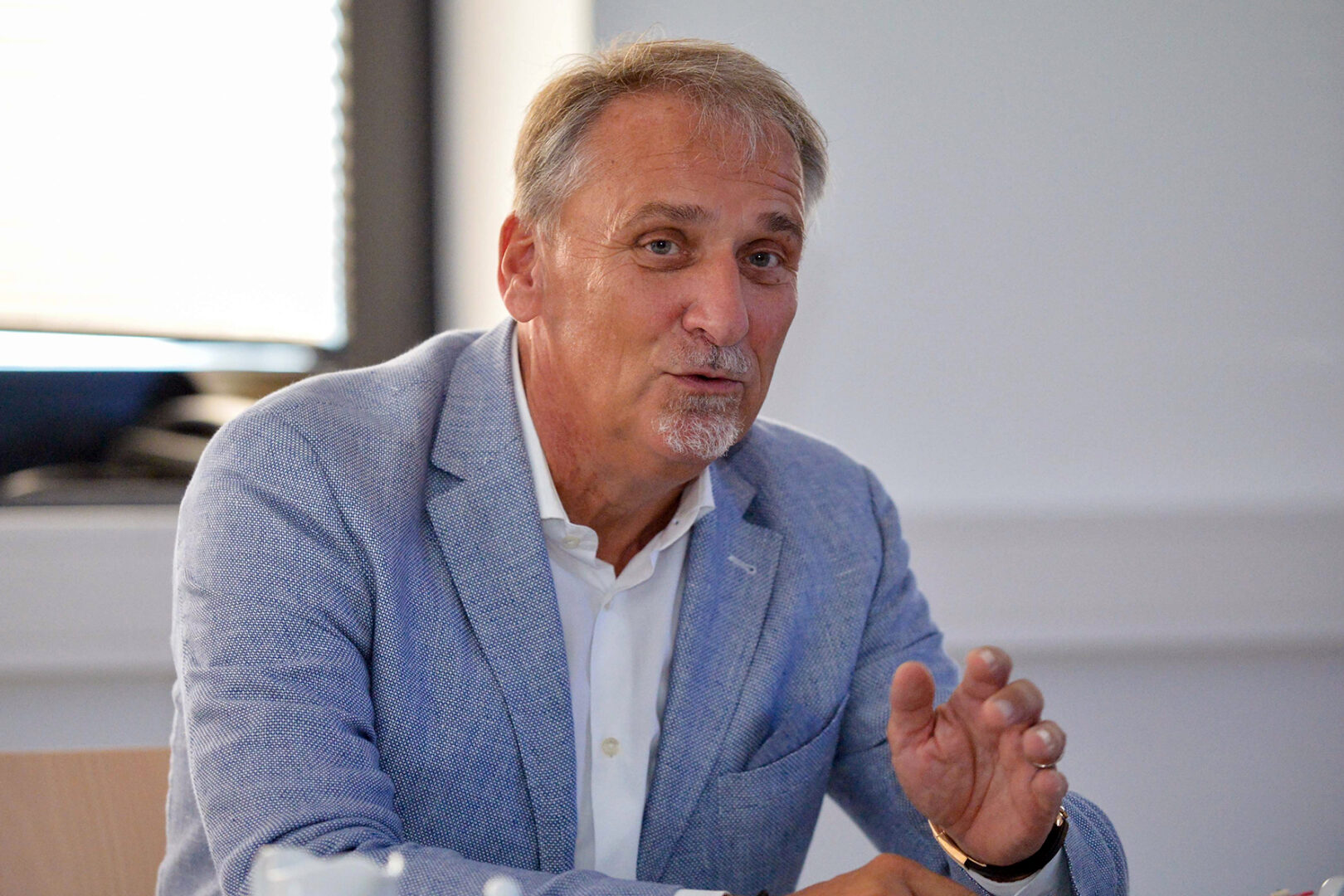
„Der Bedarf an Aluminium ist seit Langem viel höher als die Verfügbarkeit von Schrotten.“ Thomas Reuther, Mitglied des Vorstands der Trimet Aluminium SE, Bild: Trimet
Für Thomas Reuther, Mitglied des Vorstands der Trimet Aluminium SE, ist die bestmögliche Verwendung von Schrotten seit langer Zeit ein fester und wichtiger Bestandteil der Aluminiumproduktion. Trimet entwickelt, produziert, recycelt, gießt und vertreibt an sieben Produktionsstandorten moderne Leichtmetallprodukte aus Aluminium.
Herr Reuther, der Recyclingrohstoff hat in unserem Beispiel mehrere Aufbereitungsschritte und viele Arbeitsstunden hinter sich. Lohnt sich dieser Aufwand für Sie und die Kreislaufwirtschaft?
Thomas Reuther: absolut! Zum einen setzten wir Aluminiumschrotte in der Produktion ein, weil es ökologische sowie ökonomische Vorteile hat und Ressourcen schont. Zum anderen lässt sich Aluminium wie andere Metalle unendlich oft recyceln. Diese Eigenschaften machen Metalle und vor allem Aluminium zu Vorzeigerohstoffen für die Kreislaufwirtschaft.
Wie viel Schrotte beziehungsweise Recyclingrohstoffe setzten Sie für die Aluminiumproduktion ein?
Reuther: In unseren Umschmelzwerken und Gießereien produzieren wir bereits Werkstoffe für höchste Ansprüche mit einem Recyclinganteil von bis zu 95 Prozent. Insgesamt haben wir für die Aluminiumproduktion in den vergangenen Jahren rund 40 Prozent Recyclingrohstoffe in der Produktion eingesetzt.
Wenn der Einsatz von Schrotten für Sie als Unternehmen ökologisch und ökonomisch Sinn ergibt, warum setzen Sie dann nicht viel mehr Aluminiumschrotte ein?
Reuther: Der Bedarf an Aluminium ist seit Langem viel höher als die Verfügbarkeit von Schrotten. Dieses Defizit wird wahrscheinlich in den nächsten Jahren noch stärker zunehmen. Insbesondere die langen Lebenszyklen von Aluminiumprodukten führen dazu, dass die Rohstoffe erst nach sehr langer Zeit erneut für den Einsatz aufgearbeitet werden können und erneut in den Kreislauf gelangen. Deshalb werden wir auch in Zukunft noch auf Primärrohstoffe angewiesen sein.