Shredder-Reststoffe aus der Automobilverwertung bestehen aus einem bunten Mix unterschiedlicher Materialien. Neben Kunststoff, Gummi und Textilfasern finden sich im ASR wertvolle nicht-ferritische Metalle wie Aluminium, Messing oder Kupfer, aber auch mineralische Bestandteile und Glas. Letztere erschweren eine effiziente Aufbereitung, wie die Jansen Shredder Recycling BV feststellen musste.
Ausgangspunkt: Ausgeklügelter Prozess mit Schwachstelle
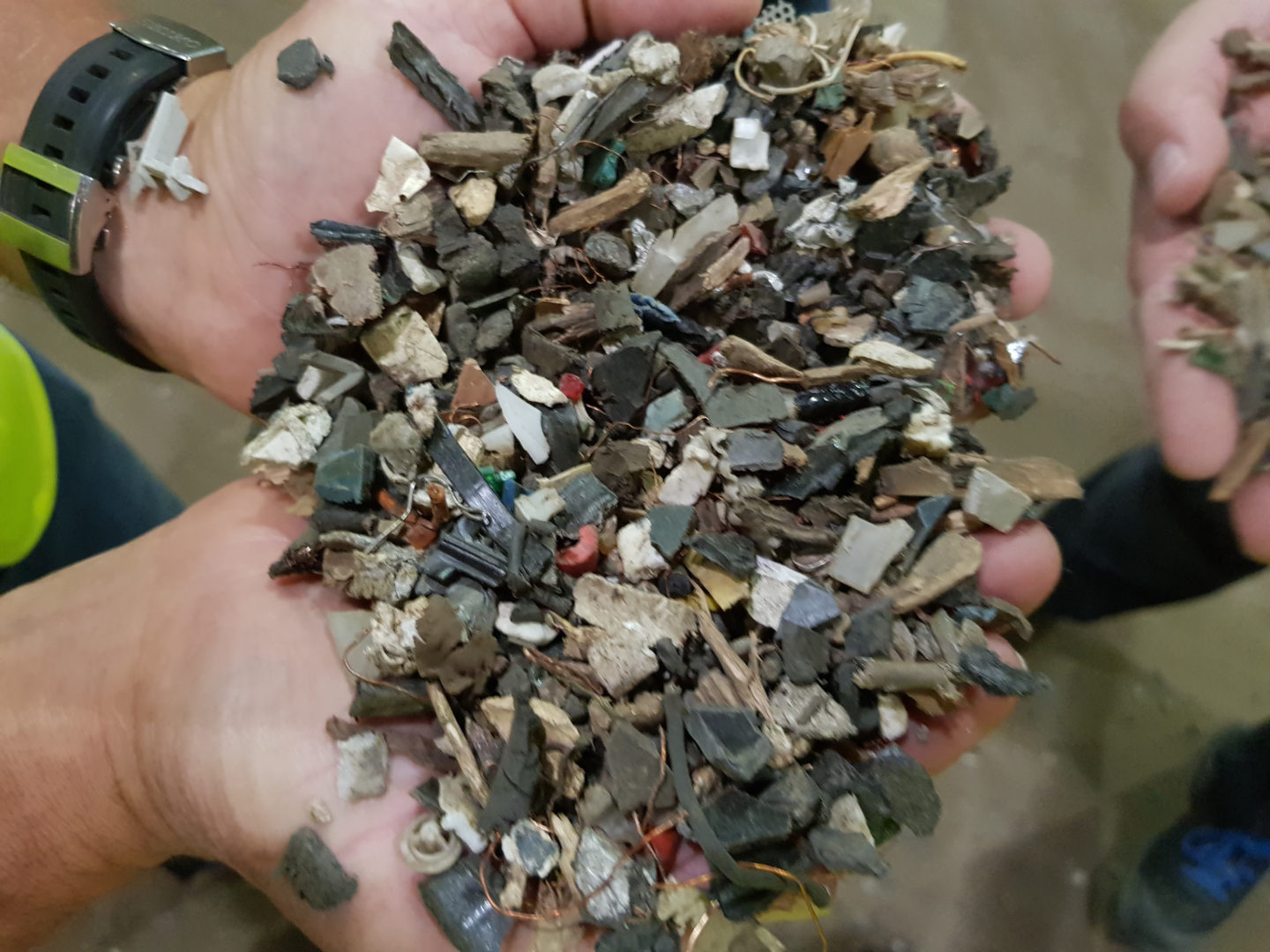
Im Aufgabematerial befinden sich wertvolle Metalle – aber auch Glas und Mineralik. Bild: BHS-Sonthofen
Ein ausgeklügelter Prozess sollte bei Jansen die größtmögliche Ausbeute an wiederverwertbaren Materialien – vor allem Metallen – sicherstellen. Mittels Querstromsichter trennte Jansen zunächst die Schwerteile ab. Die zurückbleibende Fraktion wurde im vorhandenen Granulator vorzerkleinert. Per Wirbelstromabscheidung ließ sich aus dem Material anschließend eine nicht-ferritische Fraktion gewinnen. Die nichtinduktive Fraktion enthielt jedoch neben Kunststoffen und Mineralik immer auch wertvolle Nichteisenmetalle in Form von Kupferkabeln und anderen Metallverbunden.
Um aus dieser Fraktion die restlichen Metalle zu gewinnen, setzte Jansen bisher direkt nach der Wirbelstromabscheidung Feinmühlen ein. Doch genau hier lag der Schwachpunkt bei dem sonst ausgefeilten Verfahren: Die Verschließkosten auf den verwendeten Feinmühlen fielen unerwartet hoch aus. Die Maschinen waren nicht auf die abrasiven Bestandteile ausgelegt. Glas und mineralische Bestandteile führten zu Verschleißkosten von 35 Euro pro Tonne Ausgangsmaterial. Das stand in keinem Verhältnis zu den gewonnenen Metallen. Es galt, eine neue Lösung zu finden.
Know-how aus der Gesteinszerkleinerung für ASR-Recycling
Jansen Shredder Recycling wandte sich an BHS-Sonthofen. In dem niederländischen Unternehmen war die Rotorprallmühle (Typ RPMX) aus dem Allgäu bereits bekannt. Um sicherzustellen, dass die Mühle von BHS in der Lage ist, das abrasive Material zu pulverisieren sowie die Nichteisenmetalle aufzuschließen und zu verkugeln, fuhr Jansen mit original Aufgabegut nach Sonthofen und führte gemeinsam mit den Recycling-Experten vor Ort entsprechende Versuche durch.
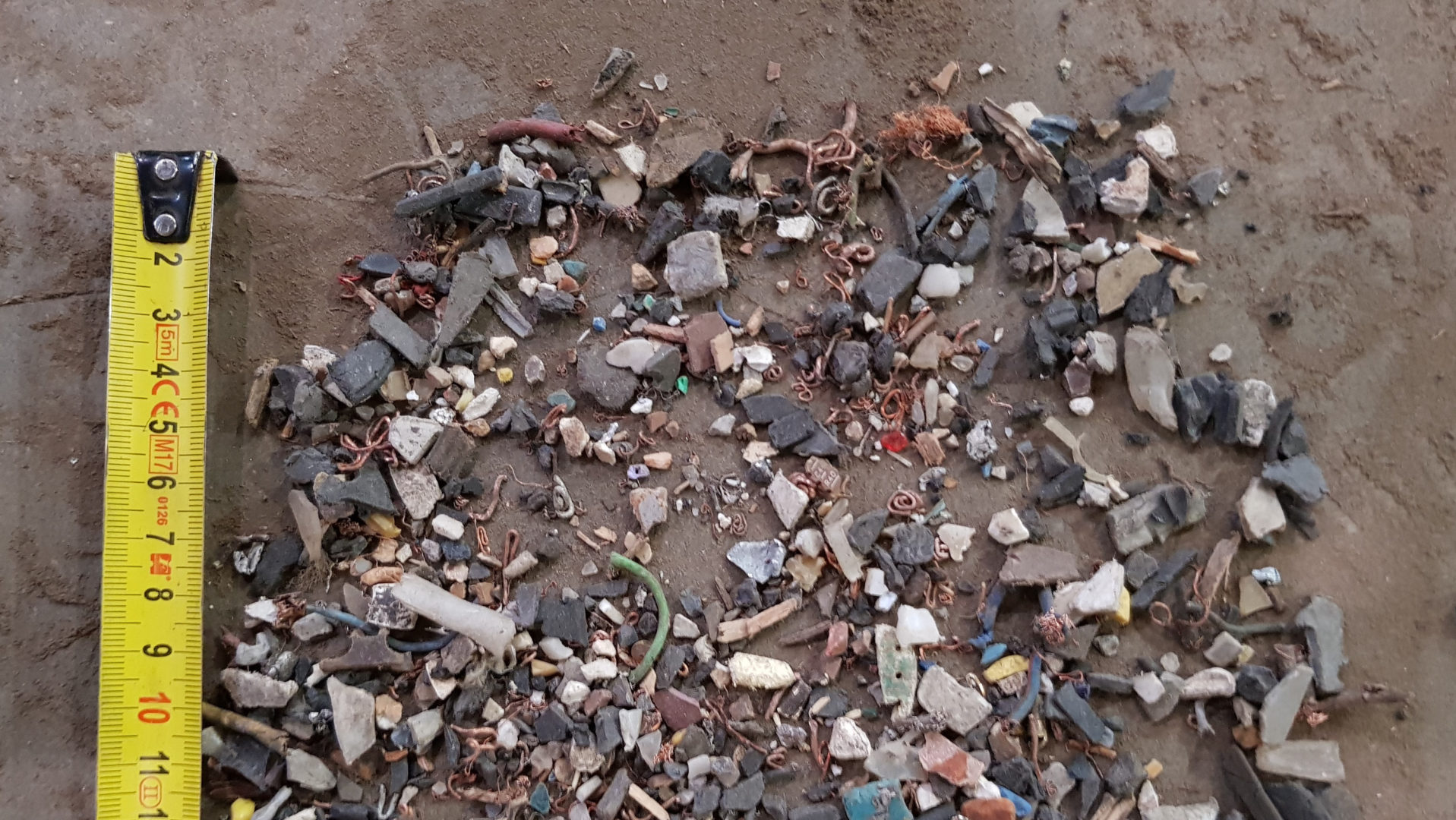
Wertvolle Kupferbestandteile lassen sich in der Rotorprallmühle optimal verkugeln. Bild: BHS-Sonthofen
Die Rotorprallmühle stammt ursprünglich aus dem Steine- und Erdenbereich. Der Einsatzbereich der hier verwendeten Modelle RPM und RPMF: die zielgerichtete Zerkleinerung von abrasiven Materialien, wie beispielsweise Flusskies. Durch ihre massive Bauweise und die Verschleißteile aus Chromhartguss ist auch die speziell für Recyclinganwendungen weiterentwickelte RPMX äußert widerstandsfähig – und damit wie geschaffen für die Aufbereitung der ASR-Fraktion, wie sie bei Jansen Shredder Recycling vorkommt.
Und tatsächlich: Das Ergebnis überzeugte. Die Mühle zerstörte Glas und Mineralik zuverlässig. „In vielen Fällen genügt es, das Material einmal über unsere RPMX laufen zu lassen, um auch die gewünschte Verkugelung zu erreichen und das Material auf Lufttrenntischen separieren zu können,“ erklärt Nikolas Kaufeisen. Area Sales Manager im Geschäftsbereich Recycling & Umwelt bei BHS-Sonthofen. „Entspricht die Verkugelung nach einem Durchlauf noch nicht den Ansprüchen, kann das Material ein zweites Mal über die Rotorprallmühle laufen.“ In Moerdijk entschied man sich gegen eine Rückführung des Materials, und dafür, den letzten Verkugelungsschritt in der bereits vorhandenen Feinmühle vorzunehmen. „Der Zwischenschritt über die Rotorprallmühle von BHS hat die Wirtschaftlichkeit des Gesamtprozesses deutlich gesteigert,“ berichtet Hans Brekelmanns, Geschäftsführer bei Jansen Shredder Recycling. „Insgesamt konnten wir die Verschleißkosten so um 75 Prozent senken.“
Seit März 2019 ist die Rotorprallmühle bei Jansen Shredder Recycling BV in den Prozess zur ASR-Aufbereitung integriert. Der gesamte Prozess hat an Effizienz gewonnen. Auch die Beratung durch die Experten von BHS überzeugte: Weitere gemeinsame Projekte sind bereits geplant.